Manganese is probably the biggest cause of discolouration of treated water and resulting customer dissatisfaction in the public water supply. An understanding of how manganese impacts water supply networks can help you manage this issue.
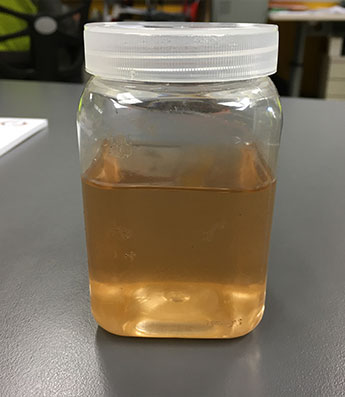
The Drinking Water Standards of New Zealand have a Guideline Value (GV) of 0.04mg/L for manganese. The intent of this GV is that if treated water manganese levels are below this then there will be no water discolouration and no staining of laundry or whiteware. However, our view is that this GV is too high. Systems which have manganese levels in the range 0.03-0.04mg/L will have episodic issues with discoloured water and we recommend that a value of <0.02mg/L is targeted to avoid these issues.
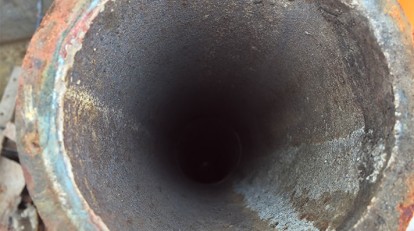
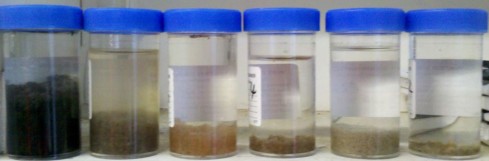
If you are having discoloured water issues the first thing to do is test your source water and the treated water leaving the treatment plant. It sounds really obvious, but suppliers can often get tied up in responding to customer complaints and miss this first critical step. The results of these tests should tell you if the cause is acute or chronic and note here that most of this article is equally applicable to iron as well.
With this information you can start to plan your response. A huge amount of time and resources can be wasted by being reactive, so taking some time to plan and coordinate your actions will give your customers the best result and reduce your stress levels. To assist with planning, we’ve put together some actions that you should work through for both acute and chronic issues.
Responding to acute issues
If you have more than one source, check all your sources for manganese and maximise abstraction from the source with the lowest levels of manganese. Even co-located bores can have different levels of manganese, so it is worthwhile checking.
Your options are limited if you don’t have manganese treatment in place and you have manganese in your only available source water. If you have granular media filtration you could consider adding a chlorine dose point, and possibly a base (e.g. lime and caustic) dosing point, prior to your filters. This will rapidly (within 1-3 days) initiate the coated media process whereby a manganese dioxide layer forms on the media which provides subsequent catalytic removal of manganese. It’s a robust and reliable process provided a free chlorine residual of at least 0.1mg/L is maintained in the filtered water.
If you have manganese removal treatment such as green-sand filtration, or the coated media process detailed above, and your treated water manganese is elevated then check the following; your pre-filter pH (target 7-7.5, dependent on your coagulant), chlorine dosing equipment, chlorine dose point and chlorine analysers. If your chlorine dosing equipment is at maximum capacity and you still cannot achieve a free chlorine residual in the filtered water, then sample your source water for ammonia. It is becoming fairly common to get ammonia events in source waters and ammonia has a very high chlorine demand. Ammonia events usually last for a few days following rainfall. You might be able to install a second chlorinator under urgency or you could temporarily dose some additional sodium hypochlorite to achieve your filtered water FAC target. Do take care to monitor pH if you are dosing more chlorine than normal. You need to try and stay in the 7-7.5 range.
Check recent maintenance activities. For example, caustic washing of filters can strip the manganese dioxide coating from the media, and it will take 1-3 days to recover from this.
Responding to chronic issues
Review your treated water quality records. In particular, focus on treated water pH. A sudden change in pH and/or a variable pH that is poorly controlled can stress biofilms (which have absorbed manganese) and cause sloughing off. A sudden change in FAC can have a similar effect. If you observe these effects then concentrate on improving your process control.
Review the location of customer complaints. Are they clustered near any scheduled or unscheduled repair works? Have any changes been made to the reticulation system (e.g. valve status changes) that could cause flow reversals or flow rate changes?
If there is no immedietly obvious change in the treated water quality or reticulation system itself, you will need to plan a systematic investigation.
Collect as much information as possible from each customer who complains. What was the water like? Was it cleared by flushing? How long did it last? Were there any odours? Had the customer been absent from the property for an extended time before using the water? Check neighbouring properties. Did they have issues? If the water is still discoloured when responding, take a sample and get it tested for manganese, iron, FAC and heterotrophic plate counts (HPC).
Initiate a system wide sample programme. Start at the plant and identify key sample points in your system. These may be existing sample points, or you may need to locate new sample points based on complaints to get sufficient coverage. Test for pH, dissolved oxygen content, ORP, manganese, iron, FAC and HPC.
All this information should be collated to give you a system wide basis for a planned flushing programme. Pay close attention to dead ends and low flow areas. Test the water flushed from hydrants at 30 second intervals for the first 5 minutes of the flush. Test for manganese, iron, FAC and HPC. Use this data to fine tune your programme.